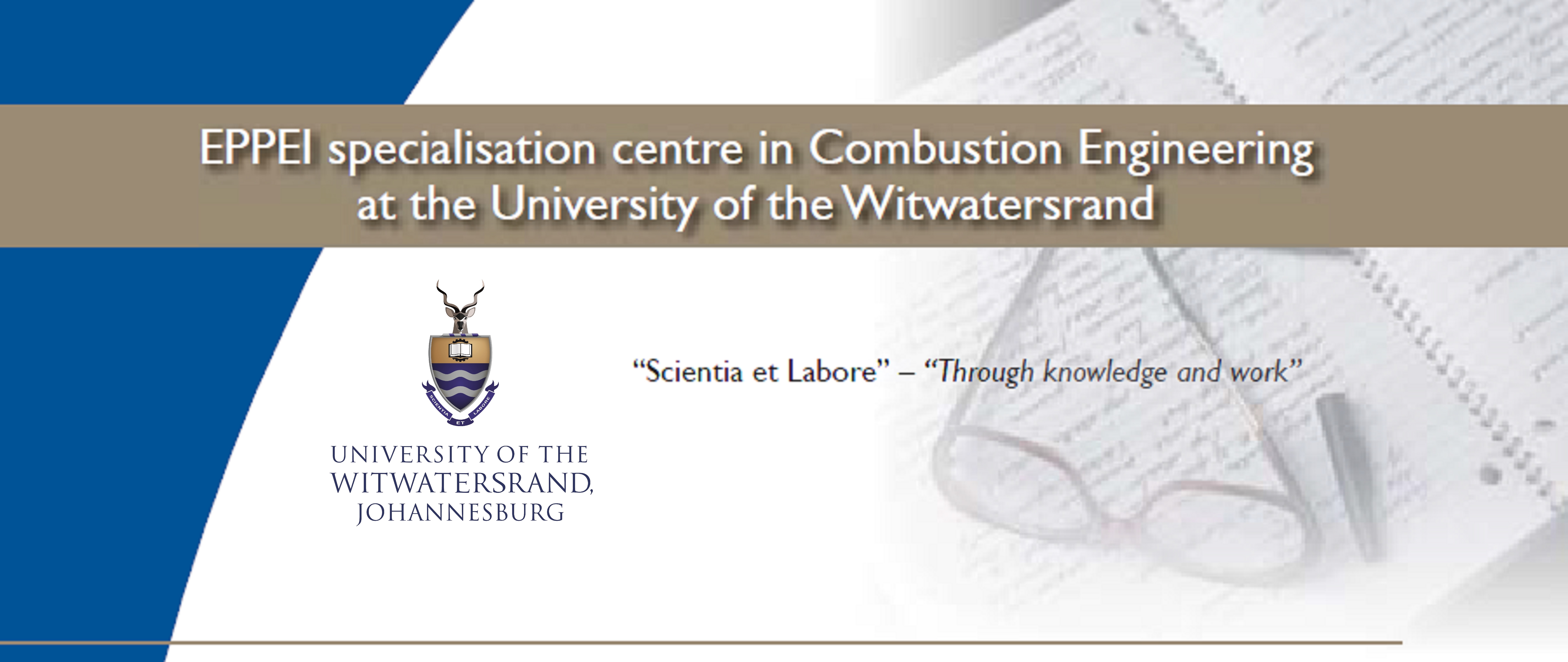
Eskom EPPEI Centre for Combustion Engineering
Measurement and instrumentation equipment installed on key components in the full
combustion systems is quite limited and sometimes inaccurate in existing plants. Additionally,
control devices have drawbacks and inaccuracies, which complicate control of the operation set
points of components and sometimes control of total boiler behaviour. It is, therefore, difficult to
monitor the combustion system online for early detection and diagnosis of abnormal situations
that cause unreliable and inefficient operation.
Local environmental standards require implementation of NOx reduction technology in all
existing and new-build plants. The low-NOx burner operation requires accurate coal and air flow
measurements for optimal control due to its operational limits and the variations in coal quality and
the need for load shifting of Eskom plant.
An urgent need exists to improve measurement and online monitoring of:
- coal mass flow and coal quality, especially ash and moisture content;
- milling plant performance to control fuel/air ratios, particle size, and mass flows;
- air streams to wind boxes, burners, and air heaters;
- heat transfer from flue gases to the air and water-steam circuit.
Pulverised fuel (PF) boiler showing four burners in operation during plant start-up
The SC strives to improve understanding of local coal impact and predicting of the effects on coal-fired
power plant. Research is focused on current Eskom requirements to:
- improve and grow a repository of skills and knowledge of existing plant;
- create skills and tools to design, operate, and maintain plants;
- ensure that future plants are cleaner, available, reliable, efficient, and safe (CARES);
- achieve world-class output in combustion engineering-related technologies;
- retain a highly skilled engineer base in Eskom to create a healthy fleet for current and future power
generation using state-of-the-art technology; - host the combustion system design intellectual property purchased by Eskom;
- attract local manufacturers to build and supply burners for the local market;
- provide a continuously improved bouquet of experimental facilities in heat transfer, combustion
technology, and thermodynamics.
To achieve its goals, the SC embarks on an applied research method ranging from fundamental research
to pilot-scale and full-scale testing, which is then taken to implementation and further development, as
outlined in the research flow chart.
Research expertise and development areas
Coal quality has a marked effect on boiler plant operation, from entering the system to the final disposal
of ash. The envelope of research is characterised by plant components such as:
- milling plant and PF piping;
- air heaters, fans, and ducting;
- pulverised fuel and oil burners; and
- boiler internal heat exchangers.
Milling plant and pulverised fuel (PF) piping
Coal combustion requires a steady stream of known quality and quantity of pulverised coal. To ensure
consistent combustion performance, measurements and process controls need to be in place. The
plant is subjected to high wear rates due to the use of high-ash coal, which causes a steady decline in
mill performance. The goal is to establish a methodology for a mill health monitoring system (MHMS)
to identify mill conditions for improved operation and required maintenance prediction. Pneumatic
transport of coal particles is an important aspect in coal delivery to burners and often causes
maldistribution and mass flow fluctuations in the piping system. To fully understand the mechanisms
influencing flow behaviour, it is necessary to model the PF transport system. This can be achieved by
means of a two-phase flow CFD analysis. In addition, measurement systems need to be identified,
tested, and implemented to measure the mass flow of air and particles and, possibly, the size distribution
of particles flowing through the PF pipes.
Air heaters, fans and ducting
Eskom’s air heaters suffer from excessive air leakages, corrosion, erosion, and blockages. Accurate
measurement of flow rates, velocity, ash, and temperature distribution, as well as gas species distribution
in the ducting and air heater itself, is necessary. Empirical performance and CFD models need to be
developed to study the impact of air leakage, acid dew point, thermal performance, as well as gas and ash
distribution. Measurements are often difficult due to large duct sizes and complex duct configurations.
Better on-site measurement techniques will be developed and implemented for improved accuracy in
performance testing concerning the boiler plant, in general. Improved monitoring of draught groups
and induced and primary air fans is needed to avoid catastrophic failures and develop maintenance
schedules based on real conditions for improved efficiency.
PF and oil burners
South African power stations are currently implementinglow-NOx burner technologies to meet more stringent
emission limits enforced by government legislation. Design and operation of burners have to be well understood. The influence of mass flow fluctuations and changes in coal quality on flame stability, pollutant formation, and combustion efficiency needs to be studied for suitable burner design, manufacturing, tuning, monitoring, and operating philosophies. The combination of poor coal ignition characteristics, lack of measurement, poor plant condition, and insufficient control leads to excessive and undesirable use of oil urner support. Once the relative influences of key parameters have been understood, the research focus will be to determine the required level of measurement accuracy on coal and industrial burners. The SC will facilitate development of an online combustion health monitoring system (CHMS) using EtaPRO, which is implemented in all Eskom’s coal power stations.
Low-NOx burner simulation results
Boiler internal heat exchangers
Energy released from combustion is transferred from combustion products to various heat exchangers
to heat water, steam, and air along the gas path. Heat transfer surfaces are exposed to high-temperature
corrosion, fly ash erosion, tube external slagging and fouling, scaling, as well as oxidation and flow Energy released from combustion is transferred from combustion products to various heat exchangers
to heat water, steam, and air along the gas path. Heat transfer surfaces are exposed to high-temperature
corrosion, fly ash erosion, tube external slagging and fouling, scaling, as well as oxidation and flowaccelerated
corrosion within tubes. This can lead to tube leaks and consequent unavailability, reduction in
efficiency, and load losses. In order to better monitor and operate the boilers to limit these degradation
mechanisms or detect them early, the condition and performance of heat exchangers, temperature, and
flow measurements on the gas and steam side are required. The research will validate and use tools
such as DIMBO and CFD to allow quick and reliable investigation into the current performance of the
boiler internals and propose measurement and monitoring techniques to be applied.
Contact
Walter Schmitz
Position: Coordinator, Professor
Dept: School of Mechanical Industrial and Aeronautical Engineering (Wits)
Education: PhD Mech. Eng.
Tel: 011 717 7047
Email: Walter.Schmitz@wits.ac.za
Reshendren Naidoo
Position: Lecturer
Dept: School of Mechanical Industrial and Aeronautical Engineering (Wits)
Education: MEng Eng. Man. (UP)
Tel: 072 246 4233
Email: reshendren.naidoo@wits.ac.za